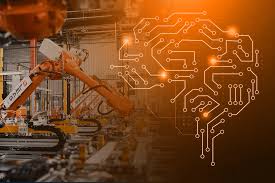
Robotic Systems Integrator In Chennai
Robotic Systems Integrator: Bridging Technology and Automation for a Smarter Future
In today's rapidly evolving technological landscape, automation is no longer a luxury—it's a necessity. As industries increasingly adopt robotics to improve efficiency and productivity, the need for Robotic Systems Integrators has never been greater. These professionals are the masterminds behind the seamless integration of robotic systems into existing infrastructure, helping businesses unlock the full potential of automation.
At Sharaa Group, we understand that automation is transforming industries such as manufacturing, healthcare, logistics, and beyond. In this blog post, we will explore the vital role of a Robotic Systems Integrator, the skills required, and why this career is pivotal in shaping the future of automation.
What is a Robotic Systems Integrator?
A Robotic Systems Integrator is a professional who specializes in designing, implementing, and integrating robotic systems into various industrial or commercial settings. Their role is to ensure that robots work seamlessly with existing systems, processes, and machinery to improve efficiency, accuracy, and productivity. This involves understanding both the mechanical and software aspects of robotics, as well as how to customize and optimize robotic systems for specific tasks and environments.
The work of a Robotic Systems Integrator is essential for businesses looking to enhance their operations with automation, whether it's for assembly lines, material handling, or complex robotic surgery.
Key Responsibilities of a Robotic Systems Integrator
Robotic Systems Integrators take on a broad range of tasks in ensuring that robotic systems operate effectively and efficiently in real-world environments. Here are some of their core responsibilities:
-
Designing and Developing Robotic Solutions:
Integrators design robotic systems tailored to a company's specific needs. They take into account factors such as workflow, space constraints, safety regulations, and production goals. This can involve selecting the right hardware, software, and sensors to meet these requirements. -
System Integration and Customization:
One of the most crucial roles of a Robotic Systems Integrator is to ensure that robotic systems work seamlessly with other systems, such as production lines, warehouse management systems (WMS), or enterprise resource planning (ERP) software. Customization is key to ensuring robots are properly calibrated to meet the needs of the business. -
Programming and Software Development:
Integrators often program the robots, develop control systems, and write the software needed for them to perform their tasks. This may involve working with various programming languages, such as Python, C++, or ROS (Robot Operating System), to create intuitive, functional automation solutions. -
Testing and Debugging:
Before robotic systems go live, integrators thoroughly test them to ensure they function as expected. They identify and troubleshoot any issues that may arise, refining the system and fine-tuning the software and hardware for optimal performance. -
Ensuring Safety and Compliance:
Safety is paramount when working with robotics. Robotic Systems Integrators are responsible for ensuring that systems comply with industry safety standards and regulations, such as those set by OSHA or ISO. They design and implement safeguards and emergency protocols to prevent accidents and ensure smooth operations. -
Training and Support:
After the robotic system is deployed, integrators often provide training to employees and operators on how to interact with and maintain the system. They also offer ongoing support and troubleshooting, addressing any issues that may arise during operation. -
Maintaining and Upgrading Systems:
Robotic systems require ongoing maintenance to ensure optimal performance. Integrators are involved in maintaining robotic systems, replacing parts as needed, and making upgrades to improve efficiency and keep pace with technological advancements. -
Collaboration with Cross-Functional Teams:
Robotic Systems Integrators frequently work with other teams, including engineers, product managers, designers, and operations teams, to ensure that robotic systems align with the overall goals of the business and integrate smoothly with other technologies.
Skills Required to Become a Robotic Systems Integrator
The role of a Robotic Systems Integrator requires a unique mix of technical expertise, problem-solving abilities, and collaboration skills. Here are some essential skills required for this career:
-
Mechanical and Electrical Engineering Knowledge:
Robotic Systems Integrators need a strong understanding of mechanical and electrical engineering principles. This knowledge is essential for selecting, designing, and integrating hardware components like actuators, sensors, and motors. -
Programming and Software Development:
Familiarity with various programming languages is crucial for designing robotic software and control systems. Languages like C++, Python, and MATLAB are commonly used, as well as robotics-specific programming platforms like ROS (Robot Operating System) and LabVIEW. -
Automation and Control Systems Knowledge:
Understanding how automation systems work, including programmable logic controllers (PLCs), supervisory control and data acquisition (SCADA), and industrial control systems, is essential for integration into existing infrastructures. -
System Integration and Troubleshooting Skills:
Integrators must be able to combine robotic systems with existing machinery and IT infrastructure. They need to troubleshoot problems that arise during integration and test phases, identifying and fixing issues with both hardware and software. -
Project Management Skills:
Given that robotic integration projects often involve coordinating between multiple teams and stakeholders, Robotic Systems Integrators need strong project management skills. This includes budgeting, scheduling, and managing timelines. -
Attention to Detail and Problem Solving:
As robotic systems are often highly complex, integrators must be meticulous in their work, ensuring every detail is accounted for. Their problem-solving skills help them identify and address issues efficiently during system implementation. -
Knowledge of Industry Standards and Safety Protocols:
Compliance with industry safety regulations is a must. Integrators must be familiar with relevant standards, such as those from ISO, IEC, and OSHA, and ensure that robotic systems meet these safety requirements.
Why Robotic Systems Integrators are Crucial for the Future
As automation continues to reshape industries, the need for skilled Robotic Systems Integrators will only increase. Here's why they are so critical:
-
Driving Efficiency and Productivity:
Robotic systems help companies reduce operational costs, increase production speed, and minimize human error. Integrators are key to making this transition seamless, ensuring that automation is both efficient and cost-effective. -
Enabling Innovation Across Industries:
From automated warehouses to robotic-assisted surgeries, the applications of robotics are vast. Robotic Systems Integrators are critical in enabling these innovations, helping industries leverage the power of robotics to stay competitive. -
Improving Safety:
By automating dangerous or repetitive tasks, robotic systems can significantly reduce workplace injuries. Integrators ensure that these systems are safe and effective, preventing accidents and improving overall workplace safety. -
Creating Custom Solutions for Complex Needs:
Each business has unique challenges, and robotic systems must be tailored to fit. Robotic Systems Integrators are skilled at customizing systems to address specific needs, whether it's for precision manufacturing, packaging, or assembly. -
Facilitating the Transition to Industry 4.0:
As businesses move towards Industry 4.0—the next stage of industrial revolution driven by smart technologies—Robotic Systems Integrators are essential in connecting machines, robots, and systems to create smarter, more connected environments.
Applications of Robotic Systems Integration
Robotic Systems Integrators work across various industries, including:
-
Manufacturing:
Integrating robots into assembly lines, packaging systems, and material handling to optimize production and reduce human labor. -
Healthcare:
Implementing robotic surgery systems and automated diagnostic tools that assist medical professionals in providing better patient care. -
Logistics and Warehousing:
Creating automated systems for sorting, packing, and transporting goods in warehouses and distribution centers. -
Agriculture:
Deploying robotic systems for tasks like planting, harvesting, and crop monitoring, increasing efficiency in farming. -
Automotive:
Integrating robots into the assembly process for precision and efficiency, as well as improving the speed of vehicle production.
Conclusion
Robotic Systems Integrators play an essential role in the automation revolution, helping businesses optimize their operations through the seamless integration of robotic technology. As industries continue to evolve, the demand for skilled integrators will continue to grow, offering exciting opportunities for professionals in this field.